sheet metal cutting operations Sheet Metal Operation: Parting -off 6. Notching: Notching operation is to cut out a portion of the sheet from its sides. And in semi notching operation metal cutting out from inside of the sheet. Sometimes, notches applied for stress relieving during the bending. So, notches created before the bending operations.
Part Duplication Guidelines And Procedure Getting Started - 2 Safety and Usage Guidelines When running an automated machine tool, safety is of the utmost importance. For proper and safe use of the CNC program and your CNC machine, the following safety guidelines must be followed: 1. Never let the machine tool run unattended. 2.
0 · sheet metal operations with diagrams
1 · sheet metal operations pdf
2 · sheet metal bending process pdf
3 · shearing operation in sheet metal
4 · restrike process in sheet metal
5 · notching process in sheet metal
6 · notching operation in sheet metal
7 · cutting clearance for sheet metal
A usinagem CNC é feita através de um comando numérico computadorizado (sigla CNC, do inglês Computer Numeric Control) que permite o controle de máquinas, sendo utilizado principalmente em fresas, tornos e centros de usinagem.
Learn about the types and processes of sheet metal cutting operations, such as shearing, blanking, punching, slotting, lancing, nibbling, perforation, piercing, . Sheet metal is a thin piece of metal between 0.006 and 0.25 inches thick. Sheet metal can be cut, bent, and stretched into various shapes through forming and cutting operations. Common forming operations include .
Step three is using the penetration method by using punch compresses, the last step is the fracturing process, the fracture is initiated. Sheet metal cutting operation you can perform by blades, chains, or wires to make . Notching is a sheet metal forming operation that involves cutting out a portion of a sheet metal workpiece to create a specific shape or profile. This process is commonly used to prepare the sheet metal for subsequent forming .Industrial sheet metal cutting operations such as this will usually incline the punch so as to reduce the maximum force needed by distributing the required force over the cutting stroke. The angle that the punch may be inclined varies from 4 to 15 degrees, however the higher the angle, the greater the magnitude of the horizontal force component .Sheet Metal Operation: Parting -off 6. Notching: Notching operation is to cut out a portion of the sheet from its sides. And in semi notching operation metal cutting out from inside of the sheet. Sometimes, notches applied for stress relieving during the bending. So, notches created before the bending operations.
sheet metal operations with diagrams
Blanking is a cutting process in which a piece of sheet metal is removed from a larger piece of stock by applying a great enough shearing force.In this process, the piece removed, called the blank, is not scrap but rather the desired part.Blanking can be used to cutout parts in almost any 2D shape, but is most commonly used to cut workpieces with simple geometries that will be .
birmingham roofing & sheet metal inc
For additional information, visit: http://bit.ly/QYucWpand don't forget to subscribe to our channel here http://www.youtube.com/user/MechanicsTips-----. 2. Sheet Metalworking Defined Cutting and forming operations performed on relatively thin sheets of metal Thickness of sheet metal = 0.4 mm (1/64 in) to 6 mm (1/4 in) Thickness of plate stock > 6 mm Operations usually performed as cold working ©2007 John Wiley & Sons, Inc. M P Groover, Fundamentals of Modern Manufacturing 3/e
Study with Quizlet and memorise flashcards containing terms like 16.1 Sheet metalworking includes both forming and cutting operations: (a) true or (b) false?, 16.2 Typical sheet-metal thicknesses are between 0.4 mm (1/64 in) and 6 mm (1/4 in). When thickness exceeds the upper limit of this range, the stock is usually referred to as which one of the following: (a) bulk stock, . Nibbling Operation in Sheet Metal The nibbling operation is a cornerstone in sheet metal fabrication, especially when detailed, intricate cuts are required. Unlike traditional cutting, where a large part of the material is removed at once, nibbling is a gradual process, ensuring a higher degree of precision and material integrity.Any mechanical cutting operation such as blanking, piercing, shearing, slitting, or trimming reduces edge ductility. . The clearances range from about 6% of the sheet material thickness for mild steel up to 16% or even higher as the sheet metal tensile strength exceeds 1400 MPa.
In a sheet-metal-cutting operation used to produce a flat part with a hole in the center, the part itself is called a blank, and the scrap piece that was cut out to make the hole is called a slug: (a) true or (b) false? . The cutting force in a sheet-metal blanking operation depends on which mechanical property of the metal (one correct .Cutting Operations - Free download as PDF File (.pdf), Text File (.txt) or view presentation slides online. This document discusses various types of cutting operations used in sheet metal working, including shearing, blanking, punching, and notching. It describes the cutting mechanism, which involves shearing action between two sharp cutting edges. Sheet metal cutting is a highly specific set of operations that mainly involves putting pressure on thin pieces of metal with specific machinery. To the contrary of its name, sheet metal cutting involves a lot of different operations that can be done with metal – and explaining the most popular ones is the goal of this article. In sheet metal processing, as many parts as possible are cut from a metal sheet to effectively use the metal without waste. The parts cut from the sheet metal are processed by a specified due-date.
Sheet Metal 1 Learn with flashcards, games, and more — for free. . worker commonly works on an assembly line with highly specialized operations. production sheet metal. . Sheet metal fabrication involves cutting and shaping operations. True. . The process of computer-aided design and manufacturing of sheet metal parts starts with computer-aided design, goes through numerical simulation unfolding, nesting, cutting, stamping, bending, and other procedures, and . Sheet metal cutting is a vital operation in the fabrication industry, with many processes used to meet varied needs and material types. The chosen process has a considerable impact on the ultimate product's quality, efficiency, and cost-effectiveness. Sheet metal cutting procedures include punching, bending, shearing, trimming, and deburring .
Study with Quizlet and memorize flashcards containing terms like Identify the three basic types of sheet metalworking operations, In conventional sheet metalworking operations (a). what is the name of the tooling and (b) what is the name of the machine tool used in the operations?, In blanking of a circular sheet metal part, is the clearance applied to the punch diameter or the .Study with Quizlet and memorize flashcards containing terms like Sheet metal working includes both forming and cutting operations. true or false, most sheet metal working operations are performed as a)cold working b)hot working c)warm working, in a sheet metal cutting operation used to produce a flat part with a hole in the center, the part itself is called a blank, and the .
Describe each of the two types of sheet-metal-bending operations: V-bending and edge bending. In V-bending, a simple punch and die that each have the included angle are used to bend the part. . which perform the cutting operation. They are attached respectively to the punch holder (a.k.a. upper shoe) and die holder (a.k.a. lower shoe). .Study with Quizlet and memorize flashcards containing terms like Typical sheet-metal thicknesses are between 0.4 mm (1/64 in) and 6 mm (1/4 in). When thickness exceeds the upper limit of this range, the stock is usually referred to as which one of the following: -bulk stock -oversized -plate -thick sheet, Most sheet metalworking operations are performed as: -cold woking -hot working . 1. Definition of sheet metal laser cutting machine (1) A sheet metal laser cutting machine is a precision manufacturing equipment primarily designed to transform flat metal sheets into intricately shaped components with high accuracy and efficiency. (2) This advanced system harnesses the concentrated thermal energy of a laser beam to perform . Metal cutting operations are the operations in which the piece of a metal or a sheet is separated by applying the force which caused the material to failure. Metal cutting is the process of removing the unwanted material from the metal in the forms of chips. . The metal cutting operations were firstly performed in the Egypt where the rotating .
Sheet metal Cutting Operations: 1: Blanking: Blanking is the operation of cutting a flat shape from sheet metal. The product punched out is called the “blank” and the required product of the operation the hole and the metal left behind is discarded as waste. 2: Punching or Piercing: Shearing is a trimming operation that involves cutting a sheet of metal along a straight line. It’s a relatively simple and fast process that results in clean, straight edges. The Shearing Process Detailed. Measurement and Marking: The sheet metal is measured, and the cut lines are marked. Setup: The metal sheet is placed into the shearing .
Shearing is used to cut sheet metal along a straight line, which is helpful when either cutting the material into smaller pieces or trimming its edges. A shearing machine has two blades that slide past each other, like giant scissors, to cut the metal. A sheet has to be placed on the machine, clamped into place, and then its upper blade is .
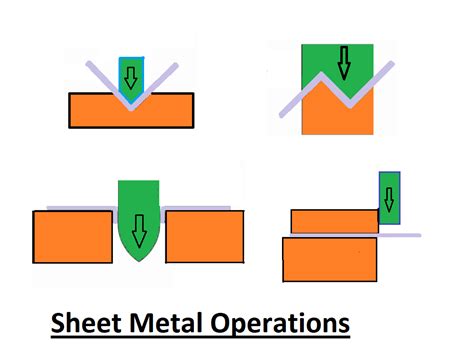
CNT Motion Systems offers surfboard shaping systems using CNC automation to boost both productivity and creativity.
sheet metal cutting operations|sheet metal operations pdf