welded sheet metal pin hole filler Any suggestions on how to treat the current pinholes in preparation for epoxy and paint? Should I drill them out and weld up the holes? Will the epoxy be sufficient to fill these in? Or should I put a skim coat of filler . Amazon.com : Universal Waterproof Camera Junction Box(4 Pack), Metal Electric Enclosure, Outdoor Camera Cover, Base Junction Box for CCTV Cameras, Bullet Security Camera Mount Bracket Hide Cable : Electronics
0 · pinhole repair after welding sheet metal
1 · pinhole patches after welding
2 · eastwood plug hole filler
_____My Favourite Tools (Through Amazon Influencer Shop): https://www.amazon.com/shop/depyrol_____Podcast:https://i.
My little mig welder has left a few pin holes in my sheet metal repair. What is good to fill these in with before laying filler over it? I've heard bondo glass is good, and I've heard . After replacing rusted areas (floor pan, bottom of doors, bottom of quarter panel) by welding sheet metal patches I find that after grinding down the welds, minute pinholes are in the welded area. What does everyone do about .
You can hook that TIG torch up to a DC machine and dial it in so fine you can literally weld razor blades. For what we're doing, you don't need the latest welding technology. . It includes everything you need to fill 30 holes and we even include a step drill bit so you can precisely drill the correct size hole so you get the . Any suggestions on how to treat the current pinholes in preparation for epoxy and paint? Should I drill them out and weld up the holes? Will the epoxy be sufficient to fill these in? Or should I put a skim coat of filler . I fixed two huge rust holes in the rear window frame section but there are a couple very tiny pinholes where I welded that just didn't get covered. I put a flash light on one side .
pinhole repair after welding sheet metal
Simply follow these steps: Step 1: Determine the center point of the patch and mark the center with punch. Step 2: Drill the hole to desired size using the smallest patch needed to .
aluminum sheet metal bend radius chart
Fix that seam or channel with POR-15's Patch sealer. This rust hole filler dries as hard as a rock, remains flexible, and is impervious to fuels & solvents. After welding on the quarter panels and grinding off the welds, can you use All Metal filler to fill the leftover pin holes? Or do you have to make sure it's completely welded? Would using lead and then All Metal a better and longer lasting solution? Thanks, Lee-----1970 ZZ502 Chevelle 1967 ZZ502 Camaro 12.04@115 1997 Yukon 4x4 13.7@98
Metal Repair Glue, Metal to Metal Glue, epoxy Glue, Metal Glue Heavy Duty Waterproof, Glue for Metal, Liquid Weld for Metal, Metal Hole Filler, Welding Glue, High Strength, Metal Weld Bond, 1.76 oz. 4.6 out of 5 stars. 23. 500+ bought in past month. .98 $ 9. 98 (.67 .67 /Fl Oz) But to use a special filler "just in case" there are pin holes in the welding? I would say, spend some more time on the welding and/or protect it from the back makes more sense. Because, I don't care what you had over that weld on the outside. If you have a pin hole in the metal and it is exposed on the back, it is GOING to fail. Clean it really well and then "ALL METAL" it ,will last forever.I wouldnt weld on weak rusty metal if you cant get to the back side of it.If there are pinholes here and there its proly paper thin all around it .Break out the welder and you may do more harm than good on pinholes not knowing how bad the other side is.The best solution obviously is to cut the bad area out .
Use some 0.30-0.35 mig wire to fill the holes. Start out on the material next to the hole to get your arc going holding the filler over the hole move the torch over to the hole as the filler melts feed it in. Have your hammer and dolly handy to keep warpage down while the weld is still hot, sand it down and finish it off.These 14-gauge welding discs are designed to fill the holes left over from shaving body trim, smoothing firewalls, or even that little rust spot in a body panel. This 29-piece kit includes sheet metal patches in several conventional hole sizes. The patch itself is slightly undersized to allow it to fit cleanly into the hole, however, the real icing on the cake is the tabs surrounding each .Although skill requirements are the highest among other welding methods, its advantages truly make TIG welding the king of sheet metal welding. MIG Welding Thin Metals. Gas Metal Arc Welding, or MIG welding, is one of the most straightforward and, therefore, most popular welding methods among beginners. Hydrogen is a notorious culprit. Dirty weld surfaces and water can contribute to that. I also noticed that it happens more with copper coated filler metal. I've had some old dogs tell me I was full of crap on the copper coating, but it was happening nonetheless. It doesn't seem to happen when using stainless filler metal.
Bondo® Extreme Metal Reinforced Filler December 2023 . Safety Data Sheet (33-2590-9) or call 1-800-494-3552. For more content, training videos and product information, visit . Remove the cap from the liquid hardener tube and using a push pin, press a hole into the dispensing end of the tube. Open the can of Extreme ller and stir the . I spent the night chasing pin holes in the motorcycle tank i tig welded. I just read on a motorcycle forum that the holes may be because I did not purge the tank with argon when I welded this? I have heard of this with titanium but never on plain steel. Any thoughts on this. lincoln tig 185 argon 100% 1/16" red tungston.035 mig wire filler 60 amps Gentlemen: Unfortunately, thanks to a previous owner, I have a '66 hood with hood pin holes in it. What's the best way to fill the holes? I would assume, straighten up the holes as best as possible; weld up the screw holes and weld in cut-to-fit sheet metal patches for the pin holes; grind and bondo as needed.
I am at a point where I am ready to put filler on some of my rear fender weld seams on my 49 Chevy. I have a dilema going at the moment. The weld seams are quite long and cut right through where the inner rear fender and exterior fender section meet. I suspect there are some small pin holes in that seam, but I am having some problems. I'm told brazing pinholes after media blasting is nearly as robust as cutting out the rot, shaping and welding in new sheet metal, but only half as time consuming (as in expensive), but only in areas that don't show.
The smaller the hole, the less effective small stitches are. In the case of filling body trim holes where you are not using filler metal, backing up the hole with a copper bar helps to absorb the heat from the weld so it doesn’t soak into the sheet metal and provides a surface to lay down some weld to fill the hole. * The weld through coatings are designed for plug welding and if you're after the best welds you can spot blast the plug holes clean before welding Im sure any heat from welding/grinding probably didnt help the undercoating I did use the everglass lite over the clean steel, and got my 1st coat of Rage over it. Actually a hybrid method would be to tack the plug in and then lead. The little sheet metal screw holes, lead also. (When body guys would pull a dent with a sheet metal screw in a slide hammer, leading up those holes was totally acceptable. however, there was no concern how things look on the back side.) Ken be careful with the patches in that you don't have any pin holes after welding. Reason being is that after a time water will get under the filler and cause trouble. I would weld the metal in and do my best to make sure there were no holes then use an .
That left me wit a bunch of 3/16" holes in about 3/32 sheet metal. Anyone got any idea how to fill in holes short of welding, maybe some kind of miracle adhesive? . and fill the hole with epoxy; ordinary Araldite works fine but any similar filler would do. Stir the epoxy in the hole to expel air and use enough to slightly-overfill the hole . Put it behind the hole and start welding around the periphery of the hole. Weld in a circle and move to the center as you finish up. The back side of the weld will be flat. If the hole you want to weld up is any bigger a good approach is to make a plug of sheet metal the size of the hole. Then just weld the plug into the hole, using tack welds.
This has been going on for years. I can not get butt welded sheet metal panels smooth. I either have low, pits (shrinkage) around the welds as shown in the pics, or I grind too much away, get pin holes in the metal and then burn thru a lot when fixing the holes- showing how thin I've made the parent metal. Mike, I have not attempted leading yet but interested. I can butt weld sheet metal with no filler rod and have a perfect fitment, but can not master doing it with no warpage. I used a Henrob welder to do that but pretty much gave up on it becasue of the warpage. . but often find "pin holes" when I can get a light behind my weld. My . Try a UV patch to fix holes in metal without welding if you want a more long-lasting and permanent method of repairing holes. . Use a putty knife or applicator supplied with the whole kit for the covering purposes with epoxy filler. You can also use the putty knife to press the epoxy. . Ensure that the sheet metal extends over the metal . For thin sheet metal welding it can be 30 ampere while for thicker (e.g. 1/8” square groove weld)- it can go up to 220 ampere for example. GMAW-S gives low heat and makes it easy to use in all positions on sheet metal, low carbon steel, low alloy steel, and stainless steel sheet metal from 25 gauge (0.02 inch or 0.5 mm) to 12 gauge (0.1 inches or 2.6 mm).
After preparing the area to be welded, Elliott went about tack welding the filler plate in place with his TIG welder. A few deft taps with a body hammer had the filler plate fitting perfectly—after that the welding was completed and then ground smooth. We caught master metalman Kev Elliott plugging the gas filler hole in an F-100.OP should carbon-gouge the weld out. Grinding can smear the metal overtop the porosity holes and the contaminants which caused the porosity. Gouging will reveal the holes without smearing the metal, and a cleanup with a die-grinder to ensure no carbon or melted contaminants remain from the arc-gouge, and possibly upsize the weld if they have to gouge deep to remove the .
My thought for the pin holes was to back them up with sheet copper will running a bead to help prevent blowing through. I've read that works for welding shut drilled holes. I have no experience with mig other than reading various forums. I've done some gas welding with varing degrees of success. I've soldered all my life. Then after the edges are welded, finish either with autogenous welding the ends of the pin(s) and holes or use pins slightly shorter than the assembly thickness to permit real "plug welds." Even with pins installed I think the halves of the welded assembly will likely be found to have shifted a little. Welding = distortion in my book. =====.
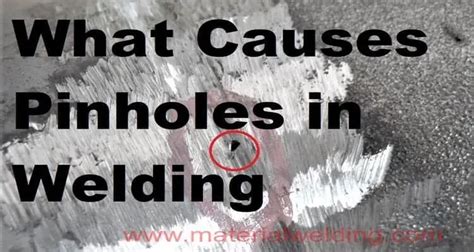
Generous Storage Capacity: 120-gallon size accommodates large storage needs effectively. Weather-Resistant Material: Made from all-weather HDPE for durability and longevity outdoors. Secure Storage: Lockable lid safely protects stored items from theft or weather elements.
welded sheet metal pin hole filler|pinhole patches after welding