sheet metal forming theory For each primary class of processes, such as forging, rolling, extrusion, wiredrawing, and sheet-metal forming, it explains how finite element analysis (FEA) can be applied with great precision . This fabric features a stunning watercolor design of pumpkins in warm, inviting colors that will add a touch of charm to any project. The metallic accents give the fabric a subtle shimmer, making .
0 · sheet metal hole to form diagram
1 · sheet metal forming yield
2 · sheet metal forming tools
3 · sheet metal forming processes
4 · sheet metal forming mechanics
5 · sheet metal forming dimensions
6 · sheet metal forming
7 · sheet metal form height formula
Classic wrought iron, wrought aluminum, and steel outdoor furniture made in Texas, USA. Collections include seating arrangements, dining, bar height, and firepit tables.
This chapter first introduces sheet metal forming processes, including their industrial importance. The principal strain increments in uniaxial loading are analyzed using .
the forming process, and the fact that dimensional variation is introduced at each bend, dimensioning in a single direction parallels the process and helps to control tolerance .This unique textbook features fundamentals and analyses of metal forming processes supported by 200 worked numerical examples. It provides rigorous detail on the three all-important groups of metal-forming processes: bulk-metal . Sheet metal forming (SMF) is a key technology to manufacturing lightweight thin-walled complex-shaped components. With the development of SMF, numerical simulation and theoretical modelling are promoted to enhance .
For each primary class of processes, such as forging, rolling, extrusion, wiredrawing, and sheet-metal forming, it explains how finite element analysis (FEA) can be applied with great precision .SHEET METAL FORMING P. B. MELLOR and A. PARMAR University of Bradford, West Yorkshire, United Kingdom ABSTRACT The paper surveys the application of plasticity theory . This chapter is intended to provide a concise introduction to plastic flow theory and the mechanics of sheet metal forming. The influence of material properties on sheet metal .It also discusses the formability of sheet steels and alloys, describes the effects of friction and lubrication, and explains how various sheet metal forming presses work and how to determine operating forces, stiffness, and other variables for .
Sheet metal forming, also known as precision sheet metal forming, is a crucial process in the manufacturing industry. It involves transforming flat metal sheets into desired shapes through mechanical and .It provides rigorous detail on the three all-important groups of metal-forming processes: bulk-metal forming, sheet-metal forming, and sheet-bulk-metal forming. Theory of metal forming is presented by discussing deformation . In these models, it was assumed that the principal directions of orthotropy of the sheet metal remain orthogonal during deformation. Another model for sheet metal forming proposed in (Vladimirov et al., 2010) uses the standard multiplicative formulation with hyperelasticity and structural tensors to characterize anisotropy.
Sheet metal forming is a very important process in industry to create a wide variety of goods. The analysis of local ductility and residual stresses is important both to assess the viability of the manufacturing process and the reliability of the resulting elements in service. . The theory should use exactly-integrable (conservative) elastic . A main ingredient of finite element simulations for sheet metal forming in industry is a robust continuum-based computational algorithm for large strain elastoplasticity which includes both elastic and plastic anisotropy, as well as mixed hardening.The theory should use exactly-integrable (conservative) elastic and hardening behaviors based on physically motivated . This paper presents a constitutive equation for anisotropic inelastic deformation rate applied to sheet metal forming based on recently developed invariants for nonlinear orthotropic elastic–inelastic material response. These invariants are based on Eulerian evolution equations for microstructural vectors that characterize directions of anisotropy and elastic deformations .SHEET METAL FORMING P. B. MELLOR and A. PARMAR University of Bradford, West Yorkshire, United Kingdom ABSTRACT The paper surveys the application of plasticity theory to sheet metal forming problems and attempts to highlight those areas where knowledge is lacking. From an engineering standpoint the most valuable analyses
The classical theory of folded developables suggests that curved crease folding can be applied to sheet metal of high strength to manufacture parts with complex geometries. However, its application has been limited to sheet metals with low strength and requires grooving or perforation of the material at the fold lines. Applying the geometrical concept otherwise .
ºõ³ .Metal casting being one of the most eminent". The main motive of this course is to make you understand the METAL FORMING (Mechanical working of metals) in greater detail without taking much of your time. The prime focus here is the rolling process. However, extrusion, drawing, forging, Sheet metal etc. will also be covered.Q 1989 Pergamon Press plc APPLICATION OF HILL'S NEW YIELD THEORY TO SHEET METAL FORMING-PART I. HILL'S 1979 CRITERION AND ITS APPLICATION TO PREDICTING SHEET FORMING LIMIT JIANSHE LIAN,* DAJUN ZHOU* and BERNARD BAUDELETt *Department of Metal Materials Science, Jilin University of Technology, Changchun, Jilin, People's Republic of .
sheet metal hole to form diagram
Introduction to Metal Forming Technology : Download: 2: Classification of Metal Working Processes : Download: 3: Behavior of Materials : . Sheet metal operations-I : Download: 38: Sheet metal operations-II : Download: 39: Powder metallurgy forming-I : . Introduction to theory of plasticity and flow curve : Download Verified; 12: True stress .Sheet Metal Forming: Fundamentals describes the changes that occur in sheet metals during forming operations and explains how to model and analyze them using computational techniques. It begins with a review of sheet forming practices followed by an in-depth discussion on the fundamentals of plastic deformation and its role in the forming process.
In a typical sheet metal forming practice, material points may experience cyclic loads; for example, bending–unbending on the die shoulder and reverse bending-unbending at the punch. In this case, transient cyclic behavior of the material must be modeled properly for a realistic simulation of the sheet metal forming process and subsequent .
The theory-guided DNN could also be applicable to other sheet metal forming processes. It provides an alternative method for compensating springback with significantly shorter development cycle and less capital cost and computational requirement than traditional compensation methods in sheet metal forming industry.Explanation: The best result is obtained, and the process of sheet metal forming will be easiest if the surface area of sheet to be drawn is high, and thickness is low. Sanfoundry Global Education & Learning Series – Mechanical Metallurgy. The mechanism of sheet metal laser shock semi-die forming is complicated, which involves many subjects and intricate influencing factors. Different combinations of laser parameters and sheet metal parameters can lead to different forming effects. Through theory analysis and experiment research, we can come to the following conclusions: (1)
Sheet metal forming technologies have been intensively studied for decades to meet the increasing demand for lightweight metal components. To surmount the springback occurring in sheet metal forming processes, numerous studies have been performed to develop compensation methods. However, for most existing methods, the development cycle is still considerably time . Sheet metal forming is widely used in a multitude of industries across the world; these industries include automotive, aerospace, electronics, telecommunications, lighting, construction, energy sector, and food-packaging industries (see Fig. 9.1).It has been learned in Chap. 1 that sheet metal forming refers to those metal forming processes that involve no or a . In order to achieve reliable but cost-effective crash simulations of stamped parts, sheet-forming process effects were incorporated in simulations using the ideal forming theory mixed with the three-dimensional hybrid membrane and shell method, while the subsequent crash simulations were carried out using a dynamic explicit finite element code. Example solutions .
Critical Dimensions Sheet Metal Forming – Outside dimension should be used unless the inside dimension is critical. - 3 - . Counter sinks – A counter sink can be put in sheet metal by both machining and/or punching. Each of these methods give the finished part different characteristics. The cross sections of the(Sheet Metal Forming Process) 1. . ทฤษฎีการงอ (Bending Theory) ในการขึ้นรูปโลหะโดยการงอขึ้นรูปนั้น เราต้องให้แรงแก่ชิ้นงานทั้งนี้ เพื่อให้ชิ้นงานนั้น .In this book, the theory of engineering plasticity is applied to the elements of common sheet metal forming processes. Bending, stretching and drawing of simple shapes are analysed, as are certain processes for forming thin-walled tubing. Where possible, the limits governing each process are identified and this entails a detailed study ofinvestigate the influence of plastic anisotropy on sheet metal forming processes such as stretching and deep-drawing. The analysis is based on the deformation theory and Hill's theory of plastic anisotropy. The numerical results are compared to experiments. It is shown that the neglect of the
Sheet Metal Stamping Dies Die Design and Die-Making Practice. by Vukota Boljanovic. 224 Pages, 6.00 x 9.00 x 0.60 in. Paperback; ISBN: 9780831134631; Availability: Print On Demand; Publication Date: July 2012; .95. BUY EDUCATORS: REQUEST AN EBOOK REVIEW COPY. Description ; About the Author;
sheet metal forming yield
sheet metal interview questions and answers pdf
APPLIED METAL FORMING; 1 Characteristics of Metal Forming; 2 Important Metal Forming Processes; 3 FEA of Metal Forming; 4 Theory; 5 Reduction and Proportions of the Plastic Zone; 6 Deformations from the Velocity Field; 7 Technological Tests and Physical Simulation; 8 Flow Stress Data; 9 Formability and Workability; 10 Friction and Friction .
M–K theory is commonly employed to predict local necking phenomena or evaluate forming limit strain, and it is a common method to calculate the forming limit curve (FLC) . In sheet metal stretch forming, deformation instability is mainly in the form of shearing; in the extrusion or stamping forming, the deformation instability is mainly in . Sheet metal forming (SMF) is an important manufacturing process to form structural thin-walled parts in modern industry. To improve the forming quality, the defects that appear during the SMF process should be given sufficient attention. . Although this strain gradient theory has its advantages, it has not been widely used. A widely used .
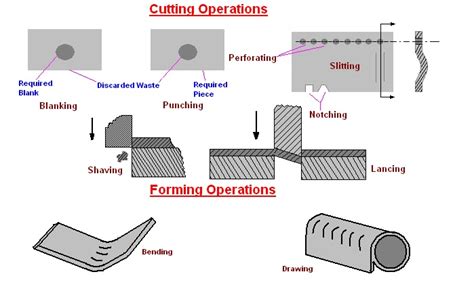
sheet metal jobs in houston tx

sheet metal forming tools
$175.00
sheet metal forming theory|sheet metal forming mechanics