edge to hole distance in sheet metal Sheet Metal Fabrication is the process of forming parts from a metal sheet by punching, cutting, stamping, and bending. 3D CAD files are converted into machine code, which controls a machine to precisely cut and form the sheets .
$24.99
0 · sheet metal rib design guidelines
1 · sheet metal fabrication design guide
2 · sheet metal extruded hole design
3 · sheet metal drawing standards
4 · sheet metal drawing dimensioning
5 · sheet metal corner relief chart
6 · sheet metal bending guide pdf
7 · minimum flange length sheet metal
Here at V-Dub Store, we carry the most comprehensive and systematic selection of Volkswagen generator and alternator conversion kits and parts for VW Type 1 engines. Find a variety of stands, straps, pulleys, complete pulley kits with belts and hardware, gaskets, covers, and more.
The minimum distance between hole/slot edge to bend edge avoid metal distortion, deformation, and fracturing. The recommended minimum distance between hole /slot edge to bend in sheet metal parts is three times the sheet thickness plus bend radius.K Factor in sheet metal bending is a constant used to calculate sheet metal .Sheet Metal gauge chart converts sheet thickness from gauge to mm or inch. .
3. The minimum distance between the hole or slot and the edge of the sheet should be three times of sheet thickness. Min. Edge-to-hole distance= 3 x thickness. 4. If the custom sheet metal fabrication design has semi-pierced .
It is recommended that the minimum distance between the extruded holes to part edge should be at least three times the thickness of sheet. Certain distance should be maintained between two extruded holes in sheet metal designs. If extruded holes are too close it .Sheet Metal Fabrication is the process of forming parts from a metal sheet by punching, cutting, stamping, and bending. 3D CAD files are converted into machine code, which controls a machine to precisely cut and form the sheets .Holes should be placed away from the curl at least a distance of the radius of the curl plus the material’s thickness. Bends should be at least 6 times the material’s thickness plus the radius of the curl. The maximum depth a countersink may have is .6 times the material’s thickness.
Outlined below are the minimum distances to be maintained between a gusset and other features like edges and holes in sheet metal components. These guidelines are calculated considering the material .The minimum distance between hole/slot edge to bend edge avoid metal distortion, deformation, and fracturing. The recommended minimum distance between hole /slot edge to bend in sheet metal parts is three times the sheet thickness plus bend radius.Edge bulging-restrictive tolerances on V bends may result in edge bulging—provide bend relief accordingly. Hole-to-form-distance from hole-to-form—to avoid hole distortion, place holes no less than 2.5 times the material thickness + bend radius from the bend itself. 3. The minimum distance between the hole or slot and the edge of the sheet should be three times of sheet thickness. Min. Edge-to-hole distance= 3 x thickness. 4. If the custom sheet metal fabrication design has semi-pierced or extruded holes, the distance from the edge or bend to them should be three times of sheet thickness.
It is recommended that the minimum distance between the extruded holes to part edge should be at least three times the thickness of sheet. Certain distance should be maintained between two extruded holes in sheet metal designs. If extruded holes are too close it .
sheet metal rib design guidelines
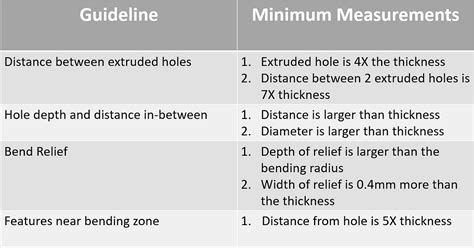
Sheet Metal Fabrication is the process of forming parts from a metal sheet by punching, cutting, stamping, and bending. 3D CAD files are converted into machine code, which controls a machine to precisely cut and form the sheets into the final part.Holes should be placed away from the curl at least a distance of the radius of the curl plus the material’s thickness. Bends should be at least 6 times the material’s thickness plus the radius of the curl. The maximum depth a countersink may have is .6 times the material’s thickness.
utility box vs junction box
Outlined below are the minimum distances to be maintained between a gusset and other features like edges and holes in sheet metal components. These guidelines are calculated considering the material thickness and the specific features involved, aiming for a balanced and efficient design. To avoid workpiece failure, DFM guidelines recommend a minimum distance (D1) from hole to the sheet edge equal to at least the plate thickness (T); we recommend a safe design zone of 1.5 to 2T. Also, when piercing multiple holes, we recommend a spacing between holes (D2) greater than 2T.Factors like bend radius and feature-to-feature cut distances should be considered. Be sure to follow design requirements and tolerances in this guide to ensure parts fall closer to design intent. Why Use Sheet Metal? Sharp edges will be broken and deburred by default.
nd slots depend on the bend radius and metal thickness. For instance, if the thickness is 0.914mm or thinner, the hole should be at least 1.574mm from the edge and 3.175mm away if t. e thickness is thicker than 0.914mm to avoid distortion. Spacing hole appropriately also helps i.The minimum distance between hole/slot edge to bend edge avoid metal distortion, deformation, and fracturing. The recommended minimum distance between hole /slot edge to bend in sheet metal parts is three times the sheet thickness plus bend radius.Edge bulging-restrictive tolerances on V bends may result in edge bulging—provide bend relief accordingly. Hole-to-form-distance from hole-to-form—to avoid hole distortion, place holes no less than 2.5 times the material thickness + bend radius from the bend itself.
sheet metal fabrication design guide
3. The minimum distance between the hole or slot and the edge of the sheet should be three times of sheet thickness. Min. Edge-to-hole distance= 3 x thickness. 4. If the custom sheet metal fabrication design has semi-pierced or extruded holes, the distance from the edge or bend to them should be three times of sheet thickness.It is recommended that the minimum distance between the extruded holes to part edge should be at least three times the thickness of sheet. Certain distance should be maintained between two extruded holes in sheet metal designs. If extruded holes are too close it .
Sheet Metal Fabrication is the process of forming parts from a metal sheet by punching, cutting, stamping, and bending. 3D CAD files are converted into machine code, which controls a machine to precisely cut and form the sheets into the final part.Holes should be placed away from the curl at least a distance of the radius of the curl plus the material’s thickness. Bends should be at least 6 times the material’s thickness plus the radius of the curl. The maximum depth a countersink may have is .6 times the material’s thickness.
Outlined below are the minimum distances to be maintained between a gusset and other features like edges and holes in sheet metal components. These guidelines are calculated considering the material thickness and the specific features involved, aiming for a balanced and efficient design.
To avoid workpiece failure, DFM guidelines recommend a minimum distance (D1) from hole to the sheet edge equal to at least the plate thickness (T); we recommend a safe design zone of 1.5 to 2T. Also, when piercing multiple holes, we recommend a spacing between holes (D2) greater than 2T.Factors like bend radius and feature-to-feature cut distances should be considered. Be sure to follow design requirements and tolerances in this guide to ensure parts fall closer to design intent. Why Use Sheet Metal? Sharp edges will be broken and deburred by default.

sheet metal extruded hole design


using junction box to extend wiring
utility trailer steel storage boxes
Spotted some of our street equipment that's in need of some TLC? We know things can happen, and we're here to help put things right. If you've noticed a problem with one of our street cabinets, cables or pits recently, we'd like the .
edge to hole distance in sheet metal|sheet metal rib design guidelines