sheet metal 90 degree bend When trying to make a good 90 degree bend with sheet metal, there's more than on way home. Just make sure your method can accommodate improvisation.
We have unattractive electrical boxes on the back of our house. We build a simple sliding wall to hide electrical boxes! This tutorial will show you how to build a wall that slides over when you need to access your boxes and slides right back when you don't!
0 · sheet metal bending strength
1 · sheet metal bending drawing
2 · sheet metal bending diagram
3 · sheet metal bending chart
4 · sheet metal bending angle chart
5 · radius of regular 90 bend
6 · large radius sheet metal bending
7 · calculate bend radius sheet metal
Watson Cream Fabric Wrap Gold Metal Frame Accent Chair Product Specifications Dimensions: 30"L x 34"W x 29"H Care Instructions All spills should be treated promptly for best results and ease of removal.
Did you size the sheet of metal to take into consideration the stretching of the metal at the bend? If you do a 90-degree bend, the metal will stretch and shrink the thickness of the metal. See more Improve your metal fabrication with Amada's 88° and 90° bend allowance chart. Get precise results and optimize your process. Download now.
They apply bend functions to a simple, single-bend part, bent past 90 degrees complementary, to show how the complementary or included angles are applied in the OSSB and ultimately to a layout. The part in Figure 4 is bent . Our comprehensive online sheet metal bending calculator is an essential tool for precision metalworking, enabling you to swiftly and accurately determine critical parameters for sheet metal bending operations. For a 90-degree bend angle, the metal must be bent to an acute angle (less than 90 degrees) and allowed to spring back to its finished position, a difficult task given the fact that a press ram typically travels vertically only. When trying to make a good 90 degree bend with sheet metal, there's more than on way home. Just make sure your method can accommodate improvisation.
Use SendCutSend’s bending calculator to input your desired material and the units of measurement for your design to get the calculated bend allowance and bend deduction for your part before sending it to our lasers. .When developing flat length for 90 degree bends always make sure the dimensions are outside to outside. Using the example to the right let us say the material thickness is .050 and the bend . A 90-degree bend sheet metal is a metal sheet that has been bent at a 90-degree angle. This type of bend is commonly used in the fabrication of metal components, such as brackets and enclosures. To create a 90-degree bend, the sheet metal is placed on a bending brake and clamped into place.
It refers to the additional length of material required to accommodate the bend in the metal sheet. Understanding and accurately calculating bend allowance is essential for ensuring that the final dimensions . In a sheet metal part, if I have two planar faces on different height I can use a double bend option of the bend-tool to connect them from two edges. If the edges of the planes are facing the same direction I can use "90 degree" . The bend allowance is an approximation of this bend's total length (our arc length calculator is the perfect tool to calculate the length of a curved line segment).. Usually, your supplier will have a bend allowance chart for each type of bend and material, such as a 90-degree bend deduction chart (we will cover bend deduction later on in the text).How to do Precision Sheet Metal Flat Pattern Layout. No part of this publication may be reproduced, or transmitted, . 90 Degree Bends. . Using the example to the right let us say the material thickness is.050 and the bend radius is .032. Our bend allowance would be: (.0078 x .050 + .01743 x .032) .
I'm trying to put corner trim on a home built truck camper, I have this 1/16" 1.5"x.15" angle laying around that's just bent sheet metal. I'm trying to decide the best method for bending it to a radius that will fit the contour of the front corner.The only exception is the feature called "Sheet Metal Gusset" but I doubt that is what you're looking for here. . The physical bracket I am trying to model has a very intentional shallow 'crease' that goes around a 90 degree bend. Probably done before the bend was created.
Table 1-10 Rebound angle at 90-degree air bend. Material r/t Thickness t(mm) <0.8: 0.8~2 >2: . To achieve higher accuracy, it is recommended to opt for a small bend radius while designing rounded corners of sheet metal bends. Avoid using large arcs as much as possible, as depicted in Figure 1-23, as they are difficult to produce and control . If a bending radius different from the plate thickness is required, a special die must be used for processing. When the sheet metal drawing calls for a 90-degree bend with a particularly small bending radius, the sheet metal should first be grooved and then bent.. Special press brake tooling, such as punches and dies, can also be used.VEVOR Box and Pan Brake, 24-Inch, 0-130 Degrees Sheet Metal Bending Brake, Portable Metal Bender with 20 Gauge Low Carbon Steel 14 Gauge Aluminum Capacity, 5 Adjustable Fingers for Metal Bending . 0-90 degree bends, easy operation with two length handles, bends material up to 36". Designed for bench top mounting or mount using "C" clamps . Assume we have a metal sheet with a thickness of 2 mm, a bend radius of 3 mm, a bend angle of 90 degrees, a K factor of 0.3, and an inside radius of 3 mm. We need to calculate consequently the bend deduction.
C90 bend forms a 90-degree bend in Lysaght CUSTOM ORB® corrugated sheets, forming continuous corners with seamless joins between walls & roofing. . Our C60 Bend (the sheet is bent over by 60 degrees) . No. Microscopic examination of sections of metal after bending have determined there is no damage. Anything over 90° will have to manually enter the bend deduction. Calculating Bend Deductions for Over 90 Degree Angles. These gauge tables are only for bends up to 90 degrees, but you can use these tables to calculate the proper bend deduction for almost all bends over 90 degrees: 1. Using Excel, open one of the All Metals Fabricating bend . Here is an example of how to make a 90-degree segment bend made out of sheet metal
precision machined parts plam city
Both compression and tension occur when bending sheet metal. The inside radius of the bent metal is in compression, or being squeezed together. . For a 90-degree bend angle, the metal must be bent to an acute .
sheet metal bending strength
I currently have a part made using the sheet metal process in Inventor. I wish to change the bend from the thickness to a perfectly 90 degree (0 mm) bend, but I keep getting errors. Is this possible to do, or will I have to remake the .
For this example, using 0.119” Mild Steel and bending at 90°, we will have a bend deduction value of 0.194” for each bend which is where we get the total length of 17.612. You can find the bend deduction value at the bottom of this page in . In this week's episode Lennart will show you HOW TO BEND THE FLANGE BELOW 90 DEGREES.The most frequently asked question about sheet metal is: "Why is it not . Upon punch removal, the part has a tendency to spring back in the center, which causes the bends to "toe in." This method works well with materials that exhibit a great deal of springback. If the metal permanently deforms in the center bowed area, it may be necessary to push the part back flat in order toachieve a 90-degree angle (Figure 4).
precision cnc turn part aluminum metal kinetic art in stock
Also is a crucial factor in sheet metal fabrication. In a 90-degree bend, the setback value is equal to the bend radius plus the thickness of the metal sheet. . Suppose you have a sheet metal piece with a thickness of 2mm, a bend radius of 5mm, and a bend angle of 90 degrees. Using the formulas provided: Setback: 5mm+2mm=7mm. Bend Allowance . The bending deduction in Solidworks is only used for the calculation of 90-degree bends in sheet metal. However, it can also be used for the calculation of non-90-degree sheet metal unfolding, but the bending deduction value for non-90-degree bending needs to be used according to the bending coefficient table. The most frequently asked question about sheet metal is: "Why is it not possible to bend the flange below 90 degrees?". The answer is quite simple the bend is often set as ‘’Tangent’’ If you set it to either "Inner Virtual Sharp" or "Outer Virtual Sharp" then it becomes possible to create a bend below 90 degreesBend Radius. In a bent sheet-metal part, the Bend Radius is the radius of the bent metal where the punch meets the part. In an air-bending process, exact 90 degree angles are not possible to manufacture. There will always be a radius on the bend, as shown below:
The bend allowance and bend deduction are two measures that relate the bent length of a piece of sheet metal to the flat length. The bend allowance describes the length of the neutral axis between the bend lines, or in other words, the arc length of the bend. Therefore, the bend allowance added to the flange lengths is equal to the total flat . HOW TO MAKE SHEET METAL ELBOWS 90degree in INVENTOR 2018Like the other comment said, the minimum bend radius will reduce this effect but it will still be there regardless. If you have a load hanging I suggest using a beam style system where you have a vertical piece of steel taking the bulk of the load. . Why are 90 degree inside corners structurally weak? upvote . Sheet metal for small vacuum .Click Insert Bends (Sheet Metal toolbar) or Insert > Sheet Metal > Bends.; In the PropertyManager, under Bend Parameters:. Click a face or edge on the model for Fixed Face or Edge.The fixed face remains in place when the part is flattened. Set a value for Bend Radius.; Under Bend Allowance, select from: Bend Table, K-Factor, Bend Allowance, Bend Deduction, .
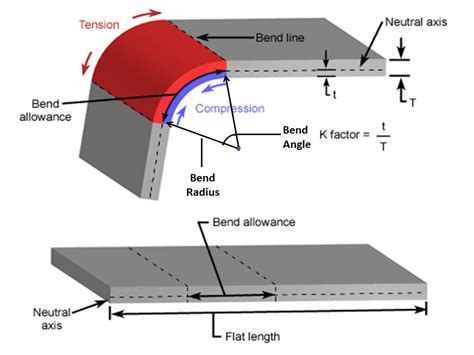
sheet metal bending drawing
WBE Sheet Metal, Inc. designed, engineered & installed Architectural Louvers, Sunscreens at the Ancillary Bldgs & Entrances, Stainless Steel Metal Panels, SS Grilles, SS Fire Cabinets, SS.
sheet metal 90 degree bend|sheet metal bending drawing