2024 sheet metal bend radius The bend radii listed are standard minimum for manufacturing for aerospace and space applications. Commercial sheet metal radius are created with less concern for stresses . Over 30 years of CNC experience and the pursuit for Excellency is the major drive at CNC Custom Machining & Fabricating Inc. We target at precision and workmanship, we guarantee that whatever parts are made in CNC Custom Machining & Fabricating Inc. will exceed your expectations and requirements.eMachineShop offers CNC machining, sheet metal fabrication, 3D printing, injection molding and various finishing options. Simply upload your design, enter your specifications and get a .
0 · sheet metal bend radius guide
1 · sheet metal bend radius formula
2 · sheet metal bend radius calculator
3 · sheet metal bend deduction chart
4 · maximum thickness sheet metal bending
5 · how to calculate bend radius
6 · bend radius sheet metal chart
7 · bend radius definition sheet metal
Order parts and accessories for all types of CNC machines. Cutting tools, workholders, toolholders, measurement and calibration devices, and more.
RECOMMENDED MINIMUM BEND RADII FOR 90-DEGREE COLD FORMING OF SHEET The radii listed are the minimum recommended for bending sheets and plates without fracturing in . Your best bet when designing formed parts is to use the industry standard bend radius of 0.030”. This measurement ensures consistent, high-quality parts with solid structural integrity. We use 0.030" for all material .
The bend radii listed are standard minimum if manufacturing for aircraft and aerospace applications. Since commercial sheet metal bending can be done with less concern for .For this layout example, use the minimum radius chart in Figure 2 to choose the correct bend radius for the alloy, temper, and the metal thickness. For 0.040, 2024-T3 the minimum . The bend radii listed are standard minimum for manufacturing for aerospace and space applications. Commercial sheet metal radius are created with less concern for stresses .
Use Xometry reference tables for sheet and aluminium to find out which bend radius is the most suitable for your sheet metal projects The bend tolerance is basically the allowable radius you can form aircraft sheet before it starts to crack. In most cases if you are unable to form in the original temper you will have to .
The bend radius refers to the inner radius of curvature in a bent metal part, where ‘t’ represents the material thickness. This parameter is crucial in sheet metal fabrication and structural design.
The default bend radius in SOLIDWORKS is 0.100”, a specification that requires specialty tooling to achieve. We recommend changing the bend radius to 0.030”, the industry standard for sheet metal with a thickness of up to .RECOMMENDED MINIMUM BEND RADII FOR 90-DEGREE COLD FORMING OF SHEET The radii listed are the minimum recommended for bending sheets and plates without fracturing in a standard press brake with air bend dies. Other types of bending operations may require larger radii or permit smaller radii. Your best bet when designing formed parts is to use the industry standard bend radius of 0.030”. This measurement ensures consistent, high-quality parts with solid structural integrity. We use 0.030" for all material thicknesses up to 0.125" (⅛") and increase the bend radius for thicker materials.
Consider what minimum bend size you require (Only consider lines that meet your minimum bend requirement). You may choose any bend radius on this line(s). If you have multiple options, optimize your choice.
The bend radii listed are standard minimum if manufacturing for aircraft and aerospace applications. Since commercial sheet metal bending can be done with less concern for stresses caused during forming operation, the radius can be near zero for thin sheet metal.For this layout example, use the minimum radius chart in Figure 2 to choose the correct bend radius for the alloy, temper, and the metal thickness. For 0.040, 2024-T3 the minimum allowable radius is 0.16-inch or 5⁄32-inch.The bend radii listed are standard minimum for manufacturing for aerospace and space applications. Commercial sheet metal radius are created with less concern for stresses created during forming and radii can approach zero (sharp internal corner) for . Use Xometry reference tables for sheet and aluminium to find out which bend radius is the most suitable for your sheet metal projects
The bend tolerance is basically the allowable radius you can form aircraft sheet before it starts to crack. In most cases if you are unable to form in the original temper you will have to anneal to the O temper, form your parts then re-heat treat.
The bend radius refers to the inner radius of curvature in a bent metal part, where ‘t’ represents the material thickness. This parameter is crucial in sheet metal fabrication and structural design. The default bend radius in SOLIDWORKS is 0.100”, a specification that requires specialty tooling to achieve. We recommend changing the bend radius to 0.030”, the industry standard for sheet metal with a thickness of up to 0.125”. For thicker metals, we can help you determine the appropriate bend radius. To set a bend radius in SOLIDWORKS:RECOMMENDED MINIMUM BEND RADII FOR 90-DEGREE COLD FORMING OF SHEET The radii listed are the minimum recommended for bending sheets and plates without fracturing in a standard press brake with air bend dies. Other types of bending operations may require larger radii or permit smaller radii.
Your best bet when designing formed parts is to use the industry standard bend radius of 0.030”. This measurement ensures consistent, high-quality parts with solid structural integrity. We use 0.030" for all material thicknesses up to 0.125" (⅛") and increase the bend radius for thicker materials.
Consider what minimum bend size you require (Only consider lines that meet your minimum bend requirement). You may choose any bend radius on this line(s). If you have multiple options, optimize your choice.
The bend radii listed are standard minimum if manufacturing for aircraft and aerospace applications. Since commercial sheet metal bending can be done with less concern for stresses caused during forming operation, the radius can be near zero for thin sheet metal.For this layout example, use the minimum radius chart in Figure 2 to choose the correct bend radius for the alloy, temper, and the metal thickness. For 0.040, 2024-T3 the minimum allowable radius is 0.16-inch or 5⁄32-inch.The bend radii listed are standard minimum for manufacturing for aerospace and space applications. Commercial sheet metal radius are created with less concern for stresses created during forming and radii can approach zero (sharp internal corner) for .
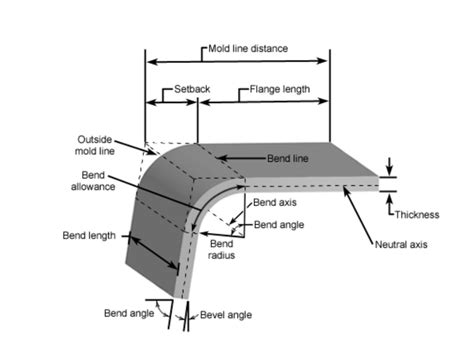
Use Xometry reference tables for sheet and aluminium to find out which bend radius is the most suitable for your sheet metal projectsThe bend tolerance is basically the allowable radius you can form aircraft sheet before it starts to crack. In most cases if you are unable to form in the original temper you will have to anneal to the O temper, form your parts then re-heat treat. The bend radius refers to the inner radius of curvature in a bent metal part, where ‘t’ represents the material thickness. This parameter is crucial in sheet metal fabrication and structural design.
sheet metal bend radius guide

precio hora mecanizado cnc
pre fabricated exterior metal wall
Millennium Metalcraft, Inc. Manufacturer providing Sheet Metal Fabrication, CNC Machining - CNC Milling, Industrial Finishes, Laser Cutting, Custom Metal Bending, Professional Welding, OEM Contract Manufacturing Nationwide Made In USA
2024 sheet metal bend radius|how to calculate bend radius