blanking sheet metal Dive into the intricacies of sheet metal blanking, from its pivotal role in manufacturing to tips for entrepreneurs and emerging trends. The most common size screw to use in an electric box is a 6-32 flathead screw. For heavier applications, like ceiling lighting and ceiling fans, an 8-32 screw will work better. Ground screws in electrical boxes are always 10-32 and must be painted visibly green.
0 · sheet metal flat length calculation
1 · semi piercing in sheet metal
2 · perforating operation in sheet metal
3 · how to calculate blanking force
4 · difference between shearing and blanking
5 · difference between blanking and stamping
6 · blank size calculator sheet metal
7 · blank length calculator
If you have a set of calipers you can measure the thickness of the existing metal and then order what you need. Here's some of the common gauges and corresponding .
sheet metal flat length calculation
Punching blanking and piercing are sheet metal shearing operations to modify existing blank. Similar machines but different punch and . What Is Sheet Metal Blanking? In sheet metal blanking, you will use punch and die system to extract suitable part from a large sheet metal. The extracted piece is the blank . Learn about sheet metal blanking, a method of cutting or shearing shapes from metal sheets. Find out the types, steps, benefits, and tips of this process, and how it is used in various industries.
Dive into the intricacies of sheet metal blanking, from its pivotal role in manufacturing to tips for entrepreneurs and emerging trends.
Blanking is a metalworking process involving cutting a metal workpiece into a predetermined shape, a foundational step in creating high-quality metal components. In this ultimate guide, you will discover the 6 key steps in the .
Piercing, punching, and blanking are crucial processes in sheet metal fabrication, and understanding the differences is essential for achieving precise and efficient operations. . In this guide, you will find all information you are looking for about sheet metal blanking. Whether you want to learn about the actual process, benefits, failure mechanism or compare it with other processes – you will find . Specialized tool steel, known as a blanking die, is used to cut metal out. This die is custom-made to punch out the desired shape from the metal sheet and is installed in a metal .
Sheet metal blanking is a foundational fabrication technique that enables precise cutting and optimized material usage. An efficient blanking process directly contributes to product quality and cost-effectiveness. In this guide, we’ll .
Punching blanking and piercing are sheet metal shearing operations to modify existing blank. Similar machines but different punch and die are used to perform these operations. In this article, we will discuss how blanking punching, and piercing operations are different from one another. From the basics of metal blanking to advanced techniques, this guide covers it all. Learn about the equipment used, materials processed, and applications of metal blanking. Read on for the ultimate guide.
What Is Sheet Metal Blanking? In sheet metal blanking, you will use punch and die system to extract suitable part from a large sheet metal. The extracted piece is the blank and one machine operation can blank multiple sheets simultaneously. Sheet metal blanking is a critical process in metal fabrication that involves the cutting or shearing of a shape from a metal sheet. This method plays a significant role in industries such as automotive, aerospace, and construction, .Dive into the intricacies of sheet metal blanking, from its pivotal role in manufacturing to tips for entrepreneurs and emerging trends.Blanking is a metalworking process involving cutting a metal workpiece into a predetermined shape, a foundational step in creating high-quality metal components. In this ultimate guide, you will discover the 6 key steps in the blanking process that are essential for achieving high precision in sheet metal products. Read on to unlock more!
Piercing, punching, and blanking are crucial processes in sheet metal fabrication, and understanding the differences is essential for achieving precise and efficient operations. The processes offer several benefits, including high precision, dimensional accuracy, surface quality, and cost efficiency. In this guide, you will find all information you are looking for about sheet metal blanking. Whether you want to learn about the actual process, benefits, failure mechanism or compare it with other processes – you will find all information right here.
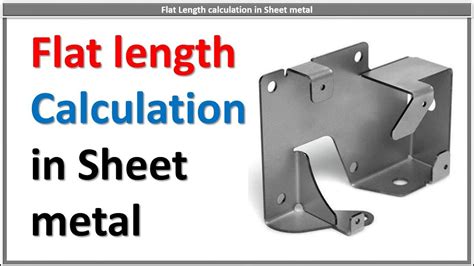
semi piercing in sheet metal
Specialized tool steel, known as a blanking die, is used to cut metal out. This die is custom-made to punch out the desired shape from the metal sheet and is installed in a metal stamping process. The die consists of two main parts: the punch and the die cavity.Sheet metal blanking is a foundational fabrication technique that enables precise cutting and optimized material usage. An efficient blanking process directly contributes to product quality and cost-effectiveness. In this guide, we’ll discover a detailed breakdown of the 9 steps involved in sheet metal blanking.Punching blanking and piercing are sheet metal shearing operations to modify existing blank. Similar machines but different punch and die are used to perform these operations. In this article, we will discuss how blanking punching, and piercing operations are different from one another. From the basics of metal blanking to advanced techniques, this guide covers it all. Learn about the equipment used, materials processed, and applications of metal blanking. Read on for the ultimate guide.
What Is Sheet Metal Blanking? In sheet metal blanking, you will use punch and die system to extract suitable part from a large sheet metal. The extracted piece is the blank and one machine operation can blank multiple sheets simultaneously.
Sheet metal blanking is a critical process in metal fabrication that involves the cutting or shearing of a shape from a metal sheet. This method plays a significant role in industries such as automotive, aerospace, and construction, .Dive into the intricacies of sheet metal blanking, from its pivotal role in manufacturing to tips for entrepreneurs and emerging trends.Blanking is a metalworking process involving cutting a metal workpiece into a predetermined shape, a foundational step in creating high-quality metal components. In this ultimate guide, you will discover the 6 key steps in the blanking process that are essential for achieving high precision in sheet metal products. Read on to unlock more! Piercing, punching, and blanking are crucial processes in sheet metal fabrication, and understanding the differences is essential for achieving precise and efficient operations. The processes offer several benefits, including high precision, dimensional accuracy, surface quality, and cost efficiency.
In this guide, you will find all information you are looking for about sheet metal blanking. Whether you want to learn about the actual process, benefits, failure mechanism or compare it with other processes – you will find all information right here. Specialized tool steel, known as a blanking die, is used to cut metal out. This die is custom-made to punch out the desired shape from the metal sheet and is installed in a metal stamping process. The die consists of two main parts: the punch and the die cavity.

ELECTRICAL INSTALLATION IMPORTANT!! Electrical installation for your cooler SHOULD be performed by a qualified electrician to ensure correct power supply, wiring, and compliance with local codes. IMPORTANT!! The enclosure does not have any predrilled holes or electrical outlets from the factory.
blanking sheet metal|how to calculate blanking force