internal bend radius sheet metal How exactly is this inside bend radius achieved? To uncover this, we must first look at the different methods of bending on a press brake: air forming, bottom bending, and coining. Coining. Note that there are three . White metal roofs are very popular in Florida! Jan 2, 2020 - Inspiration for your White Metal Roof project. See more ideas about house exterior, metal roof, house design.
0 · sheet metal bend radius guide
1 · sheet metal bend radius formula
2 · sheet metal bend radius calculator
3 · sheet metal bend deduction chart
4 · maximum thickness sheet metal bending
5 · how to calculate bend radius
6 · bend radius sheet metal chart
7 · bend radius definition sheet metal
$12.90
Bend Radii & Minimum Bend Sizes. It is most economical to use a single bend radius throughout the design, but if necessary, you can utilize multiple radii. Use this document to choose values .
In steel between 0.5 and 0.8 in. thick, grade 350 and 400 may have a minimum bend radius of 2.5 times the material thickness when transverse bending, while longitudinal bending may require a minimum bend radius that’s .
Use Xometry reference tables for sheet and aluminium to find out which bend radius is the most suitable for your sheet metal projectsRemember that the internal radii (the section formed by the punch) of any flange directly impacts the K-factor, bend allowance, and so on. Here again, though, we’ve dialed in our K-factors and found that a 0.030 in. (0.762mm) bend . How exactly is this inside bend radius achieved? To uncover this, we must first look at the different methods of bending on a press brake: air forming, bottom bending, and coining. Coining. Note that there are three . Input Material Thickness and Inner Radius: • Enter the precise sheet thickness and desired inner bend radius. • The calculator will instantly provide the K-factor, Y-factor, and neutral layer position, crucial for accurate .
sheet metal bend radius guide
Sheet Metal Bending Calculation. Bend Allowance (BA) BA = [ (0.017453 × Inside radius) + (0.0078 × Material thickness)] × Bend angle, which is always complementary. The length of the neutral axis is calculated as a bend .
Your best bet when designing formed parts is to use the industry standard bend radius of 0.030”. This measurement ensures consistent, high-quality parts with solid structural integrity. We use 0.030" for all material . The minimum bend radius of the sheet metal is affected by several factors, each of which is of specific importance in determining the most desirable degree of bend that would .
You just have to insert the characteristics of the sheet metal to be bent. . Internal bending radius (Ri):: 2.5 mm. Minimum flange (B):: 13 mm. Die opening (V): 20 mm . CONFIGURE YOUR X-PRESS . CONFIGURATOR. Now that you know the tonnage and length, you can configure your press brake with our online tool and receive a customised quote. Factors Influencing the Minimum Bend Radius. The minimum bend radius of the sheet metal is affected by several factors, each of which is of specific importance in determining the most desirable degree of bend that would prevent collapse or paper deformation. tAng factors include:. Material Type: Different materials have varying levels of ductility and tensile strength, .
sheet metal bend radius formula
The bending radius usually refers to the distance from the bending axis to the plate surface when bending metal plates, bars, etc., Which is generally called the internal bending radius. The external bending radius is usually the sum of the .
With this in mind, what is the minimum internal bend radius for a piece of sheet metal? Determining the Minimum Internal Radius for a Bend in Sheet Metal. There are a two major factors that affect how tight you can make the internal radius of a bend in a piece of sheet metal: The hardness of the metal. The thickness of the metal. Generally . In conclusion, sheet metal bend radius plays a crucial role in determining the quality and integrity of the bends. It is essential to consider factors such as material thickness, bend angle, and type of machinery used to achieve optimal results. By adhering to the recommended bend radius values and using the appropriate tooling, you can avoid .Bending radius is often used in sheet metal working. This page explains the working methods, measurement problems, and how to measure 3D shapes accurately. . (λ: lambda) at a bent point differs depending on the material thickness, hardness, bending angle, and internal bending radius. The neutral axis is believed to be located at a position .Minimum Bend Radii: The minimum bend radius data shown in these charts is measured to the inside of the bend. The bend radii listed are standard minimum if manufacturing for aircraft and aerospace applications. Since commercial sheet metal bending can be done with less concern for stresses caused during forming operation, the radius can be near zero for thin sheet metal.
sheet metal bend radius calculator
Bending Radius Bending Radius refers to the minimum radius that can be applied to a sheet metal component where its flange originates from. Bending radii are usually dictated by available tooling, and for quick and effective design work it is recommended to speak with manufacturers so that design can be done around their standard operating procedures as well as available tooling. Sheet Metal Bending Calculation. Bend Allowance (BA) BA = [(0.017453 × Inside radius) + (0.0078 × Material thickness)] × Bend angle, which is always complementary. The length of the neutral axis is calculated as a bend allowance, taken at .
Question: My co-workers and I have been reading your columns to help us understand what tooling our shop will need to avoid overstressing our materials with small dies. We air bend our 0.125-inch-thick 5052-H32 aluminum with a 1-mm punch and 16-mm die. Based on your columns, the inside bend radius should be 13 to 15 percent of the die opening. Sheet metal is popular due to its strength, durability and manufacturability. When you design for this medium, there are some guidelines that you should foll.
The data in the table above is the preferred data for reference only. In fact, the rounded corners of press brake are usually 0.3, and a small number of the rounded corners of the press brake punch is 0.5.. For ordinary low carbon steel plate, anti-rust aluminum plate, yellow copper, purple copper etc, the inner radius 0.2 is no problem, but for some high carbon steel, .
The bend radius is a critical parameter in sheet metal fabrication, dictating the minimum radius one can bend a metal sheet without significant deformations. Calculating the correct bend radius is essential for ensuring the structural integrity and aesthetic of the finished product. . Maintenance of this radius prevents internal cable damage .In sheet metal fabrication, bending is the critical operation for creating the custom parts required. Our Sheet metal is bent with a press brake or folder in order to form custom electronic enclosures and parts. . (Watch More Tech Tip Videos) An internal bend is a bend that is placed on a particular area of a part where material surrounds the .For air bending in steel/stainless we use a k factor of .4, bend radius is usually around 1T. That's good enough for a ±.031 flange length tolerance on the vast majority or our job shop work. Reply reply Sometimes I need to make parts in bended sheet metal, so I use sheet metal workbench. I have a problem: every time that I make a bend, I have to change internal bend radius (Ri) and k-factor (Kf), because FreeCAD set them to default values (Ri=1 and Kf=0,5).
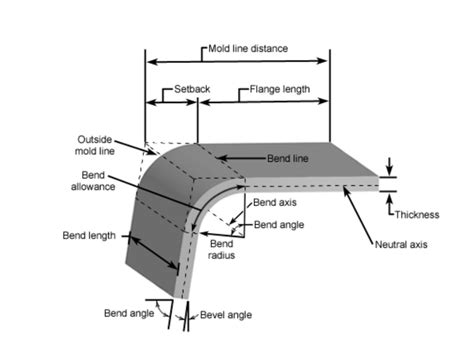
You can calculate the developed length of sheet metal parts using bend calculation tables. Editing the Default Bend Radius, Bend Allowance, Bend Deduction, or Relief Type. A Sheet-Metal1 feature in the FeatureManager design tree indicates a sheet metal part. The Sheet-Metal1 feature contains the default bend parameters.Recommended inside bend radius for sheet metal parts should be equal to material thickness. For hard materials (Stainless steel, CRCA), an inside bend radius equal to 0.65 times of sheet thickness is also enough.Posted by u/megashroom22 - 4 votes and 12 comments To achieve the correct sheet metal bend radius, it is crucial to use proper techniques, equipment, and tooling. Using the appropriate press brake and metal bending tools and following proper air bending or metal bending procedures can ensure a consistent and accurate bend radius. With careful consideration of all the factors involved, including .
sheet metal bend deduction chart

90-DEGREE COLD FORMING OF SHEET The radii listed are the minimum recommended for bending sheets and plates without fracturing in a standard press brake with air bend dies. Other types of bending operations may require larger radii or permit smaller radii. The minimum permissible radii will also vary with the design and condition of the tooling.The K-factor in sheet metal bending represents the ratio between the thickness of the metal and an invisible line called the “neutral axis.” . (BA) by using the K , Bend Radius (R), Bend Angle (A) and Material Thickness using the formula below. BA=Pi*(R+K*T)*A/180. In this formula: K represents the K-factor. BA is the bend allowance. A is .
Click Insert Bends (Sheet Metal toolbar) or Insert > Sheet Metal > Bends.; In the PropertyManager, under Bend Parameters:. Click a face or edge on the model for Fixed Face or Edge.The fixed face remains in place when the part is flattened. Set a value for Bend Radius.; Under Bend Allowance, select from: Bend Table, K-Factor, Bend Allowance, Bend Deduction, .
Sheet metal layout isn't hard. You just do it right, and it works. Draw the part with the OD of the bends marked correctly. Now, using a bend allowance table and the metal thickness with bend radius to enter the table, SUBTRACT the allowance from the OD, once for each bend. If it's tab with one bend, subtract once. An overview of bend radius for sheet metal, including types, materials, tools, and important design considerations is provided in this article. +1(213) 398 9420 +86 13922902420; [email protected]; Mon - Sat: 9:00 - 18:30; Sheet Metal Fabrication. CNC Machining . Metal Stamping. Get Instant Quote. It is important to note that the sheet metal bend radius used in fabrication efforts influences structural capacity as well as appearance in fabrication projects.Hence knowing these aspects contributes towards attaining accurate, sustainable, and aesthetic work.
maximum thickness sheet metal bending
how to calculate bend radius
H&S Antique Metal Jewelry Box for Storage - Floral Vintage Jewelry Box for Necklaces & Rings - Silver Trinket Box with Authentic Treasure Chest Design for Women
internal bend radius sheet metal|sheet metal bend radius guide