sheet metal blanking mould Definition: Blanking: This process involves punching a metal sheet to create a blank. The punched-out component is what you are interested in. Punching: Punching primarily aims to make holes in metal sheets. Typically, the slug or . Under Cabinet TV Mount | Folding Ceiling Television Mount Bracket with 90 Degree Retractable Arm | Swivel and Fold Down Compatible. This under .
0 · sheet metal blanking techniques
1 · sheet metal blanking procedure
2 · sheet metal blanking machine
3 · sheet metal blanking instructions
4 · metal blanking materials
5 · mechanical blanking of sheet metal
6 · hydraulic sheet metal blanking
7 · blanking sheet metal
Learn how ultrasonic metal welding works and the processes of ultrasonic spot welding, wire bonding, tube sealing, seam welding and wire splicing.
Definition: Blanking: This process involves punching a metal sheet to create a blank. The punched-out component is what you are interested in. Punching: Punching primarily aims to make holes in metal sheets. Typically, the slug or .
Sheet metal blanking is a critical process in metal fabrication that involves the cutting or shearing of a shape from a metal sheet. This method plays a significant role in industries such as automotive, aerospace, and .
Sheet metal blanking is a foundational fabrication technique that enables precise cutting and optimized material usage. An efficient blanking process directly contributes to product quality and cost-effectiveness. What Is Sheet Metal Blanking? In sheet metal blanking, you will use punch and die system to extract suitable part from a large sheet metal. The extracted piece is the blank .Moulds for blanking are used to cut and cold-deform any type of sheet metal: aluminium, iron, stainless steel, brass, copper or titanium. Thanks to a careful design, these moulds determine, .Step#1 Material Selection for Blanking. Step#2 Designing the Blanking Die. Step#3 Preparing the Sheet Metal. Step#4 The Blanking Operation. Step#5 Inspection and Quality Control. Step#6 Post-Blanking Processes. Conclusion. .
sheet metal blanking techniques
Sheet metal blanking is a vital metalworking process that shapes thin metal sheets into precise tolerances for numerous applications. From material selection to finishing .
Blanking is a crucial sheet metal fabrication process that involves cutting a flat sheet to create a flat piece or blank of specific shape and size. This process is essential in the early stages of .Minifaber performs metal blanking on iron, aluminum, copper, stainless steel and special alloys sheets with maximum precision and advanced technology. Metal blanking involves shaping sheet metal using punches, which deform and cut, .
1. www.moldclamps.net [email protected] 0086-17322110281 DGMF Mold Clamps Co., Ltd [email protected] Please browse our website or contact us for more articles, thank you. Sheet metal process .The blanking operation consists, in fact, in pressing onto the sheet a cutting force sufficient to separate the material along the border of the cutting unit of the mould. This type of moulding is performed using a mould formed by a punch and a .
sheet metal blanking procedure
We design and manufacture block molds, progressive molds and transfer molds for cold sheet metal processing, specializing in automotive and household appliances. Artisan heart. Our roots as an artisan company allow us, in .
Find the right provider for your wholesale sheet metal blanking mould needs. We can suply moulds for all kinds of precision manufacturing needs across all materials. Sheet metal fabrication is a comprehensive cold-working process for thin metal sheets, typically less than 6 mm in thickness. This versatile manufacturing method encompasses a wide range of operations, including shearing, blanking, bending, welding, riveting, die forming, and surface treatments.Sheet Metal punching and blanking is to use the single-chip microcomputer on the cnc punching machine to input the fabrication program (size, fabrication path, fabrication tools, etc.) of the sheet metal parts in advance, so that the CNC punching machine can use various tools, through rich NC commands Various forms of punching, trimming, forming, etc. can be realized.Sheet metal bending by mould is carried out thanks to the use of a mould mounted on presses (mechanical or hydraulic). This solution allows important time and costs optimizations. Generally, the initial investment, in order to be amortized, has to be supported by a series production.
sheet metal blanking machine
The utility model provides a high-efficient sheet metal component blanking die, which belongs to the technical field of blanking die, and comprises a bracket, an upper die assembly and a lower die body, a hydraulic cylinder is fixedly arranged at the top of a mounting frame, one end of a telescopic piece is fixedly connected with the top of the mounting frame, two ends of the .Metal blanking involves shaping sheet metal using punches, which deform and cut, and dies, which give the shape. On this page, we will deepen what metal blanking is, how it works and what service Minifaber can provide. Metal blanking is a process that requires experience and precision.
As one of the advanced metal processing methods, cold stamping mold is mainly used in sheet metal processing, so it is also called sheet metal stamping. It is a . size, and cut surface quality. It includes blanking, piercing, incision, slice and other processes. Shaping process is a stamping process in which plastic deformation is produced P.S: If you want to calculate hydraulic press tonnage, you can use our hydraulic press tonnage calculator.. Related calculator: V & U-shaped Bend Force Calculator Press Tonnage Calculation Formula. If you need to punch round, square, or any other type of hole through a given metal thickness, you’ll need to determine the punching force required to .
expensive sheet metal, slow, very high formability Technology – a brief review Forming Speed 20-1000pts/hr 7-13cycles/hr 3-8pts/hr 0.3-4pts/hr . Drawing – expensive tooling, no net thinning, quick Deep-drawing Shallow-drawing (stamping) Deep-drawing
Stamping is usually carried out on sheet metal, but can also work with other materials. The metal stamping process involves a variety of manufacturing processes, including punching, blanking, embossing, bending, flanging, and more. It can be a single-stage operation or go through a series of stages with multiple techniques. In the manufacturing industry, the sheet metal process is common, and sheet metal parts are used in many different industries, including consumer products, appliances, aircraft, and the automotive and aerospace sectors. Sheet Metal Operations. Following are the 9 different types of sheet metal operations: Shearing Operations; Blanking Operations Piercing is a shearing process in which raw metal is pierced with a machining tool, resulting in the creation of a circular or other shaped hole. As the raw metal is pierced, the metal from the newly created hole is considered .We are a company that embodies multiple skills in the field of sheet metal processing. We offer our customers all the techniques available in the sector: prototyping, moulds design and construction, 2D and 3D laser cutting, .
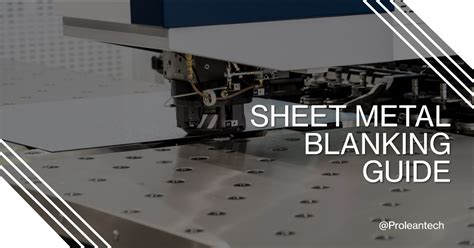
Plastic and die casting mould separator; Machining; Blog; Contacts Menu. Home. Sheet metal dies. Design and manufacture of sheet metal dies. . Universal has specialised in cold sheet metal working and offers various types of services: .A separate shearing machine or blanking equipment is required for the pre-production of blanks, and there is an additional cost of sheet turnover. . This is the cost price of a set of one meter long continuous die for ordinary sheet metal parts. The same size car mold quote plus 20%, 16666 US dollars * 1.2 = 20000 US dollars.Cold sheet metal blanking is a precision cold-working process conducted by MP at room temperature using punches and dies.This method is employed to create precise and intricate shapes. MP employs this process to produce metal parts adaptable to the automotive sector, household appliances, and other fields of application.The process offers numerous .Blanking is a basic sheet metal stamping process that uses molds to separate materials. It can be directly made into flat parts or prepare blanks for other stamping processes such as bending, deep drawing, forming.
sheet metal blanking instructions

manufacture sheet metal parts. Blanking is a common sheet metal manufacturing process used in the production from the range of small components to high strength materials. The sheet range from the 0.2-20mm thickness can be used for the applications. [1] In blanking, punch and die clearance is the important Stamping Mold is the process of creating two-dimensional part shapes from pieces of blanked or coiled sheet metal. Stamping Mold is used to transform flat metal sheets in specific shapes. Welcome to E-mold rapid manufacturing Ltd ! SEARCH. Tel : . Manufacturing process of blanking 1-Punch; 2-Mold . 2. Manufacturing process of drawing.
Metal stamping is a complex process that can include a number of metal forming processes — blanking, punching, bending, and piercing, to name a few. . Burr allowance is generally 10% of the thickness of the sheet material. To minimize instances and severity of burrs, avoid sharp corners and complex cutouts when possible. When such factors .
The invention discloses a blanking mould for sheet metal parts. The blanking mould comprises a mould shank, an upper molding board, a lower molding board, a punching convex mould and a trimming convex mould, wherein guide posts are arranged between the upper molding board and the lower molding board; the mould shank is fixedly connected above the upper molding .Drawing mold allows you to make a flat vacuum in a container seamlessly with the bottom. Forming mold. This refers to the use of various methods of forming the mold. It can be convex, curled, neck, and round edge hole flange. Compression mold. Uses strong pressure to flow and deform raw metal into the required shape.China Sheet Metal Mold wholesale - Select 2024 high quality Sheet Metal Mold products in best price from certified Chinese Mould manufacturers, China Mold suppliers, wholesalers and factory on Made-in-China.com . Fine Blanking: Multi-Position. 1 / 5. Favorites. Progressive Punching Mold for Sheet Metal. US$ 1000-15000 / Piece.
metal blanking materials
mechanical blanking of sheet metal
With a stainless steel cutting wheel or blade, can openers help you neatly access the contents inside the can without injuring you or requiring heavy effort on your part. Certain multi-function can openers can not only cut through lids but also have an attached bottle opener.
sheet metal blanking mould|sheet metal blanking techniques