typcical tolerance in sheet metal fabrication Future of tolerances in sheet metal fabrication. The future of tolerances in sheet metal fabrication is moving towards greater precision and efficiency. We anticipate the following trends: AI and Machine Learning: AI and machine .
$35.50
0 · typical manufacturing tolerances pdf
1 · types of manufacturing tolerances
2 · sheet metal tolerances pdf
3 · sheet metal tolerance table
4 · precision tolerance chart
5 · mechanical design engineering tolerances
6 · manufacturing process tolerances chart
7 · manufacturing process tolerance curve
Ratcheting open-end crowfoot wrench sets allow the wrench to rotate freely in one direction without removing the wrench head from the fastener and repositioning the wrench. They can access fasteners from the top and side and in tight spaces where .
We frequently receive RFQs for parts with tolerances that exceed what is achievable in standard fabrication. Most of these issues are related to sheet metal forming, such as achieving ±0.005 tolerance across multiple bends, which surpasses our recommended .
low voltage lighting distribution box
The manufacturing process used for specific features in sheet metal fabrication .After taking EML2322L, the students should have a tangible understanding of the tolerances associated with basic manufacturing processes used in this course (i.e. milling, turning, . Aluminum Alloy: The typical tolerance range is around ±0.1mm due to its softer nature. Stainless Steel: The tolerance range can be slightly larger, around ±0.2mm, with its higher hardness. . Various factors affect actual tolerances in sheet metal fabrication, highlighting the importance of involving your fabricator in the initial design .
A CAD jockey who understands metal fabrication makes better decisions in applying CAD tools. Let’s focus on the accuracy of things made from rolled sheet stock. . (typical tolerance of ±0.002 in.) can routinely have tighter .Future of tolerances in sheet metal fabrication. The future of tolerances in sheet metal fabrication is moving towards greater precision and efficiency. We anticipate the following trends: AI and Machine Learning: AI and machine .Comprehensive resource of fabrication tolerances and dimensional variation guidelines for sheet metal manufacturing and fabrication. Transform your team's workflow with Protocase Designer Enterprise, the game-changing design tool for . Fabrication Tolerances for Dimensional Variance in Sheet Metal and Machined Parts. Bending Tolerances .
As a designer, if you carefully consider the manufacturer's tolerances when designing - you will have a greater outcome than simply designing and assuming all parts are nominal size. • Protocase commits to supply parts to the dimensional tolerances noted in this resource, unless we have agreed to other tolerances when quoting your job.
5 Geometry-Dependent Tolerances 6 Typical Stock Size and Gauge 6 Sheet Stock Sizes and Gauge Lookup Chart 7 Stock Material Thickness Tolerances 8 Quoting Formats: 3D CAD and DXF Files . Sheet metal fabricators can “unbend” the model on their end to produce the part to specifications. In some cases, a DXF file can be used for both
Future of tolerances in sheet metal fabrication. The future of tolerances in sheet metal fabrication is moving towards greater precision and efficiency. We anticipate the following trends: AI and Machine Learning: AI and machine learning will transform how we manage and implement tolerances. These technologies analyze data from the .
What’s considered a “standard” tolerance differs in precision machining and sheet metal fabrication. A standard tolerance for precision machined parts is +/- 0.005.” A standard tolerance for sheet metal fabricated parts is much looser, ranging from +/- 0.02” to +/- 0.03.” Tolerances can also vary within parts. The typical tolerance for injection molding varies depending on factors such as the material, part size, complexity, and precision requirements. Generally, for most plastic parts, the following tolerance ranges apply: Standard Tolerances: ±0.005 inches (±0.127 mm) to ±0.010 inches (±0.254 mm) for less critical features or parts.; Tight Tolerances: ±0.002 inches (±0.051 . For instance, in CNC machining, a typical standard might be +/—0.005 in. (0.13 mm) for production runs, though precision machining can achieve tolerances as tight as +/—0.0005 in. (0.0127 mm) for critical features. . engineers can optimize the design to account for these tolerances. Sheet Metal Fabrication: Sheet metal parts are typically .
“Having a handy guide to compare your called tolerances will profoundly affect your production,” Benson explained. By a “handy guide,” Benson means a guideline specifying reasonable tolerances for a formed part, both for linear and angular dimensions, as shown in Figure 1.. “You will no longer be making unreasonable demands, and no longer will you have . In sheet metal, there are some typical defaults – with a few underlying assumptions – that we printed in the table above. . If you’re looking for tighter tolerances in sheet metal fabrication, it’s best to contact us to discuss. When we know the important factors involved in your manufacturing project, .
The tolerance might be shown as a value, a plus/minus, or, within the rules of GD&T, a combination of basic dimensions and tolerance zones (see Figure 2). Using plus/minus tolerances on dimensions (or using title block default to imply the plus/minus tolerances) is permitted as a drafting technique within ASME Y14.5 (see Figure 3). While plus . These tolerances serve as a general guide and can vary depending on the specific material, machine capabilities, and project requirements. It’s important to consult with the manufacturer of the laser cutting machine or an experienced professional to determine the appropriate tolerances for the specific materials and applications being used.This also means that tolerances in the title block of a drawing may be unnecessarily restrictive for certain dimensions and angles, while very appropriate for others. Critical Dimensions Sheet Metal Forming – Outside dimension should be used unless the inside dimension is critical. Table of Contents. 1 Surface Finish Scales for Sheet Metal Fabricated Parts; 2 Creating Beautiful Surface Finishes for Sheet Metal Fabricated Parts; 3 Surface Finish Considerations for Sheet Metal Fabricated .
Actual tolerances in sheet metal fabrication are influenced by various factors, underscoring the necessity of engaging with your fabricator at the initial stages of design. Ensuring CAD designs are aligned with Design for .
Specialize in CNC Milling, CNC Turning, 3D Printing, Urethane Casting, and Sheet Metal Fabrication Services. LinkedIn; . Typical Standard Tolerances . Typical CNC standard tolerances vary depending on the machining process, material, and the required precision for the specific part. Below are typical tolerance ranges for different CNC processes:
typical manufacturing tolerances pdf
Sheet Metal Guage Tolerances. During the rolling process the rollers bow slightly, which results in the sheets being thinner on the edges. The tolerances in the table and attachments reflect current manufacturing practices and commercial standards and are not representative of the Manufacturer's Standard Gauge, which has no inherent tolerances. .Sheet Metal +/- 0.010” – 0.020” is typical and highly dependent on geometric features like bends and weldments. Xometry recommends staying above 14 gauge for best performance and designing with common gauge thickness. As a general rule, please make sure all metal CNC parts have a minimum wall thickness of 0.030". Bending of a sheet metal part Dimensions and Tolerances. To better understand how to factor in the dimensional tolerances of each of these processes (shearing, punching and bending), here’s a sample part that we’ve designed that has all the kinds of holes and bends that you can possibly replicate in your part!
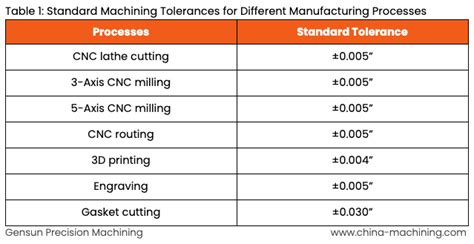
In sheet metal fabrication, the flange length (or flange height) is the distance between the bend and the part’s edge or the next feature, such as a hole or another bend. . Stick to ASM’s standard sheet metal tolerances. Or have a conversation with our sheet metal services team, and we’ll help you achieve your tolerancing goals! 8 . The design needs to account for these differences for a fabrication shop to achieve the designing engineer’s goals. Sheet metal tolerances help operators have better control over their results for more consistent production. This guide will provide an overview of sheet metal tolerances and their uses. Sheet Metal Tolerances: A Definition Sheet metal forming is a sheet metal fabrication process that manipulates metal into flat sheets into complex shapes. Employed extensively across various industries, this technique involves a range of operations such as bending, drawing, and punching. . This section delineates the typical stages of sheet metal forming, from initial design to . Commonly used flatness tolerances for metal stamping, laser and turret are shown below. . Dayton Rogers is your trusted resource for sheet metal fabrication, metal stamps, metalforming and all your manufacturing company needs. . Get a free quote today on your custom metal fabrication project. LOCATIONS MINNEAPOLIS 8401 West 35W Service .
Recommended Default Sheet Metal Tolerances Default Tolerances (Millimeters) DIM Tolerance Description A ± 0.13 Sheared Edge to Hole B ± 0.13 2 Holes on One Surface C ± 0.25 Formed Edge to Hole D* ± 0.76 Holes Across 2 Bends E* ± 0.76 Holes Across 4 Bends F ± 0.25 Sheared Edge to Bend G ± 0.38 Across 2 Bends H* ± 0.76 Formed Part Default .
types of manufacturing tolerances
A solar panel junction box is a crucial component of a solar panel system. It connects electrical components in the solar panel. It ensures that the generated electricity is distributed. The junction package is on the back of the .
typcical tolerance in sheet metal fabrication|sheet metal tolerance table