bend radius sheet metal Sheet Metal Bend Radius Guidelines Here are a few key concepts to know about designing for sheet metal Brackets, covers, cabinets, chassis, electrical enclosures. First you tack weld your sheet metal or plate. Then, what you do is weld a short bead on one end of your piece, and then weld on the other end, and then move back down to another spot away from your second weld, until you finish up .
0 · sheet metal bend radius guide
1 · sheet metal bend radius formula
2 · sheet metal bend radius calculator
3 · sheet metal bend deduction chart
4 · maximum thickness sheet metal bending
5 · how to calculate bend radius
6 · bend radius sheet metal chart
7 · bend radius definition sheet metal
Looking for industrial welding services in Morton? Our skilled professionals provide top-quality welding for construction, manufacturing, and fabrication projects. Contact us today for reliable and efficient industrial welding solutions.
Learn the factors that influence bending radius and the methods to determine the optimal bending radius for your sheet metal projects. Find bend radius charts for mild steel, stainless steel and aluminum alloys. A typical recommendation is 1t for all sheet metal parts, which means the smallest bend radius should be at least equal to the sheet thickness. For example, if the thickness of the sheet is 2mm, the minimum bend radius .The bend radii listed are standard minimum if manufacturing for aircraft and aerospace applications. Since commercial sheet metal bending can be done with less concern for .Sheet Metal Bend Radius Guidelines Here are a few key concepts to know about designing for sheet metal Brackets, covers, cabinets, chassis, electrical enclosures.
Just a few are the forming method (air forming, bottoming, or coining), the type of bend (sharp, radius, or profound radius bends), the tooling you are using, and the multibreakage of the workpiece during large-radius . We recommend a minimum bend radius of 1t for all sheet metal parts. Thus the smallest radius of any bend in a sheet should be at least equal to the thickness of the sheet. For example, if the thickness of the sheet is 1 mm, .
Sheet metal bend radius is an essential factor to consider during metal forming processes like air bending or metal bending with a press brake. The bend radius refers to the curvature of a bend and is determined by the material type, .
How to implement the industry standard sheet metal bend radius. Your best bet when designing formed parts is to use the industry standard bend radius of 0.030”. This measurement ensures consistent, high-quality parts with .When designing sheet metal parts and enclosures, it is helpful to use these values as the basis for your design. It is most economical to use a single bend radius throughout the design, but if .Use this page to choose bend values for sheet metal that are both manufacturable and meet your needs. The sheet metal bending radius is a critical value in sheet metal drawing that can be difficult to determine during the actual processing. This radius is dependent on the material thickness, the pressure of the press brake machine, and the width of .
A typical recommendation is 1t for all sheet metal parts, which means the smallest bend radius should be at least equal to the sheet thickness. For example, if the thickness of the sheet is 2mm, the minimum bend radius should be 1t which is 2mm. What is the Right Bend Radius for Sheet Metal?The bend radii listed are standard minimum if manufacturing for aircraft and aerospace applications. Since commercial sheet metal bending can be done with less concern for stresses caused during forming operation, the radius can be near zero for thin sheet metal.Sheet Metal Bend Radius Guidelines Here are a few key concepts to know about designing for sheet metal Brackets, covers, cabinets, chassis, electrical enclosures. Just a few are the forming method (air forming, bottoming, or coining), the type of bend (sharp, radius, or profound radius bends), the tooling you are using, and the multibreakage of the workpiece during large-radius bending.
We recommend a minimum bend radius of 1t for all sheet metal parts. Thus the smallest radius of any bend in a sheet should be at least equal to the thickness of the sheet. For example, if the thickness of the sheet is 1 mm, the minimum bend radius should be 1 mm.
Sheet metal bend radius is an essential factor to consider during metal forming processes like air bending or metal bending with a press brake. The bend radius refers to the curvature of a bend and is determined by the material type, thickness, and bend angle. How to implement the industry standard sheet metal bend radius. Your best bet when designing formed parts is to use the industry standard bend radius of 0.030”. This measurement ensures consistent, high-quality parts with solid structural integrity.When designing sheet metal parts and enclosures, it is helpful to use these values as the basis for your design. It is most economical to use a single bend radius throughout the design, but if necessary, you can utilize multiple radii. Use this document to choose values that are both manufacturable and meet your needs.Use this page to choose bend values for sheet metal that are both manufacturable and meet your needs.
The sheet metal bending radius is a critical value in sheet metal drawing that can be difficult to determine during the actual processing. This radius is dependent on the material thickness, the pressure of the press brake machine, and the width of . A typical recommendation is 1t for all sheet metal parts, which means the smallest bend radius should be at least equal to the sheet thickness. For example, if the thickness of the sheet is 2mm, the minimum bend radius should be 1t which is 2mm. What is the Right Bend Radius for Sheet Metal?The bend radii listed are standard minimum if manufacturing for aircraft and aerospace applications. Since commercial sheet metal bending can be done with less concern for stresses caused during forming operation, the radius can be near zero for thin sheet metal.Sheet Metal Bend Radius Guidelines Here are a few key concepts to know about designing for sheet metal Brackets, covers, cabinets, chassis, electrical enclosures.
Just a few are the forming method (air forming, bottoming, or coining), the type of bend (sharp, radius, or profound radius bends), the tooling you are using, and the multibreakage of the workpiece during large-radius bending. We recommend a minimum bend radius of 1t for all sheet metal parts. Thus the smallest radius of any bend in a sheet should be at least equal to the thickness of the sheet. For example, if the thickness of the sheet is 1 mm, the minimum bend radius should be 1 mm.
Sheet metal bend radius is an essential factor to consider during metal forming processes like air bending or metal bending with a press brake. The bend radius refers to the curvature of a bend and is determined by the material type, thickness, and bend angle.
How to implement the industry standard sheet metal bend radius. Your best bet when designing formed parts is to use the industry standard bend radius of 0.030”. This measurement ensures consistent, high-quality parts with solid structural integrity.
mixing metals throughout house
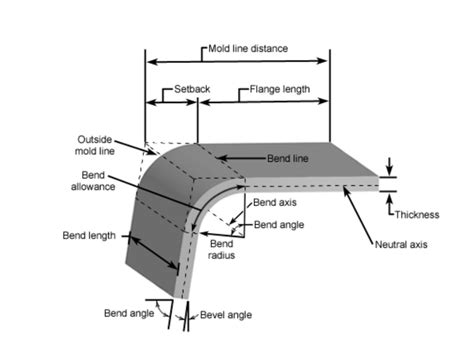
sheet metal bend radius guide
sheet metal bend radius formula

The welding of Hollow Structural Sections (HSS) does have some unique features. Unlike open sections, where welding is typically possible from both sides of an element, welding of HSS is only possible from one side, thus requiring larger weld sizes.
bend radius sheet metal|maximum thickness sheet metal bending