sheet metal coining Coining is a form of precision stamping in which a workpiece is subjected to a sufficiently high stress to induce plastic flow on the surface of the material. A beneficial feature is that in some metals, the plastic flow reduces surface grain size, and work hardens the surface, while the material deeper in the part retains its toughness and ductility. The term comes from the initial use of the process: manufacturing of coins A distribution of code 3 in box 7 of your form 1099R means that you took a distribution due to a disability. If you are under full retirement age at your work then the 1099R should show up on line 7 with W2 wages and if you were over the retirement age it will be listed on line 16 (line 12 on 1040A) as pension income.
0 · sheet metal process in impl
1 · sheet metal operations with diagrams
2 · sheet metal coining process
3 · restrike process in sheet metal
4 · lancing process in sheet metal
5 · design for manufacturing sheet metal
6 · defects in sheet metal operation
7 · coining process in metal stamping
One main job is to shield electrical connections. It guards them from things like moisture, dust and heat. The junction package provides a secure enclosure. It shields the delicate wiring and parts from potential damage. This extends the lifespan of the solar panel system.What is Array Junction Box (AJB) in solar PV modules? An Array Junction Box, AJB, is used to connect the photovoltaic strings in parallel. The combined DC power is fed to the photovoltaic inverter. It includes photovoltaic string protection, overvoltage protection and a .
Coining fabrication is a basic type of bending in which the workpiece is stamped between the punch and die. Both the punch tip and the punch actually penetrate into the metal past the neutral axis under a high amount of pressure.

Coining is a form of precision stamping in which a workpiece is subjected to a sufficiently high stress to induce plastic flow on the surface of the material. A beneficial feature is that in some metals, the plastic flow reduces surface grain size, and work hardens the surface, while the material deeper in the part retains its toughness and ductility. The term comes from the initial use of the process: manufacturing of coins In this video, I will introduce you to coining sheet metal. We will not be making coins but, that’s where the name comes from. Coining metal is the process o.
Coining produces finer details and provides a smooth surface finish to the metal work piece. Coining can be done using a gear driven press, a hydraulic press, .
Coining dies create the part's shape by squeezing the metal under extreme pressure. Coining also can reduce the metal thickness. Coins (metal currency) are created with the coining process. Sheet metal bending is a fundamental forming process that alters the geometry of a metal sheet or panel by creating angular changes along a linear axis. This versatile technique can produce a wide range of profiles, including V .Metal coining is a forging process by which very fine and intricate details can be created on the surface of a work piece. Coining may be used to control surface quality and detail on parts. Metal coining is often a finishing process for .
Sheet metal folding is bending a metal sheet to create specific angles and shapes. It involves applying force to the metal to change its geometry without altering its volume. This technique . Coining has several advantages and disadvantages. It can produce sharp, crisp corners; well-defined features; and a brilliant surface finish. Because coining uses compression to form the part, tension failure is unlikely. . Forming sheet metal can include bending, flanging, coining, embossing, stretching, curling, hemming, ironing, necking, and drawing related. Learn more here. Our Sites . FMA; . Coining is a process in which the metal .
What Is Coining? Metal coining is a forging process by which very fine and intricate details can be created on the surface of a workpiece. Coining may be used to control surface quality and detail on parts. Metal coining is often a finishing process for manufactured products. This is a flashless, precision forging operation that . ="Difference Between Coining .Sheet Metal Forming 2.810 D. Cooper !“Sheet Metal Forming” Ch. 16 Kalpakjian !“Design for Sheetmetal Working”, . • “coining” or bottoming the punch . Pure Bending Bending & Stretching σ h -Y Fully plastic σ h Y Fully plastic Y Y tension compression . Good day people! I would like some guidance in determining the diameter of a hole which is pre-pierced before countersinking by a coining process. I deal with sheet metal materials like cold-rolled steel, EG steel, stainless steel, etc. Is . Sheet metal joining technology is widely used in industries like mechanical engineering, chemical engineering, automotive, aerospace, and electrical appliances. The main methods of sheet metal joining include welding, riveting, threaded connections, and adhesion. Welding is one of the most common and crucial methods in sheet metal joining.
TOX® PRESSOTECHNIK equipment provides the highest quality marking, stamping, and embossing for your sheet metal and non-metallic parts. Get a quote today! . Sheet Metal Coining, Marking & Stamping. Solutions Overview Clinching Riveting & Joining Fastener Insertion Assembling Punching Coining. Pressing Reference projects.Below the sheet metal is a die that has a certain shape or cross-section. A punch produces a high impact force to push the sheet metal onto the die, effectively deforming it to match the die’s cross-sections. . As the name suggests, coining is a metal stamping technique in which a small piece of metal is stamped in order to take the shape .
sheet metal process in impl
The coining is a sheet metal fabrication process, its core is to use high tonnage to make metal sheets utterly fit the geometry shape of the punch and dies. This is realized by putting the metal sheet on the die and using the punch to exert much pressure. This method ensures the metal will not be deformed and bent during the bending process. Because the sheet metal is positioned between these two dies, it bends to form the shape of the dies. Coining. Also using a press brake is the bending process known as coining. Coining is a high-performance bending process that’s characterized by greater force. Like air bending, it compresses sheet metal between a top die and a bottom die. I n this blog post we will have a closer look to coining which takes place in stamping operations and the usage of new thick shell elements in AutoForm will be demonstrated. We also share the results of a Bilstein-AutoForm joint project, where the effect of coining in deep drawn cups was investigated. The results of this project were presented during Numisheet 2018 in .There are three types of bends used to form metal that any sheet metal engineer or press brake operator must be familiar with; Air Bending, Bottom Bending and Coining. Air Bending. Air Bending is the most common type of bending process used in sheet metal shops today.
value of a poker game set in a metal box
Metal stamping is a complex process that can include a number of metal forming processes — blanking, punching, bending, and piercing, to name a few. . Burr allowance is generally 10% of the thickness of the sheet material. To minimize instances and severity of burrs, avoid sharp corners and complex cutouts when possible. . Coining Coining . Sheet Metal stamping- coining and cookie bite 2. Thread starter vikas4auto; Start date Nov 2, 2017; Status Not open for further replies. Nov 2, 2017 #1 vikas4auto Mechanical. Sep 26, 2017 3 IN. Hello to All, I'm currently working on a progressive die design project.
Using excessive tonnage, coining works by hitting the material with enough force to actually thin it, thereby relieving the natural springback of the material by ruining the metal’s integrity. Coining also works only with a sharp punch, rarely with a punch carrying a radius greater than 63 percent of the material thickness.
uss mfg 1943 metal tool box
sheet metal operations with diagrams
Discover the art of sheet metal design in this comprehensive guide. Learn fundamental principles, techniques, and prospects. Dive in now! Capabilities. Sheet Metal Fabrication. . Coining: Coining is a high-tonnage procedure .Stamping includes a variety of sheet-metal forming manufacturing processes, such as punching using a machine press or stamping press, blanking, embossing, bending, flanging, and coining. [1] This could be a single stage operation where every stroke of the press produces the desired form on the sheet metal part, or could occur through a series . Coining is a precision bending technique that employs substantial force to plastically deform the sheet metal into a die cavity. During the coining process, the punch and die are pressed together with the workpiece sandwiched between them, causing the material to flow and conform precisely to the tooling geometry.
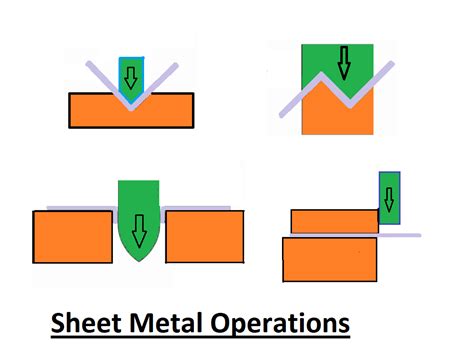
Coining is a closed-die forging operation in which all surfaces of the workpiece are confined or restrained, resulting in a well-defined imprint . Steel, Hammers, Industrial lubricants, Coining, Closed-die forging, Finishing, Metal-matrix composites, Copper. You do not currently have access to this chapter. . Sheet, Strip, and Tubing .
Coining Sheet Metal 7. Bending Sheet Metal. It is a process where you apply force to deform sheet metal into different profiles. Depending on the sheet metal bending technique, you can get: L shaped profile; U shaped profile; V-shaped profile; Of course, you can have custom profiles depending on unique design requirements.coining. slitting. 15 of 31. Term. A straight punch rapidly moves up and down into a matching die cavity making overlapping holes-> Allows intricate and large slots to be made using standard punches. . Process where sheet metal is clamped around its edges and is stretch over a die or form block. Used for large parts such as aircraft-wing skin . 3. Coining. Here’s the interesting process, which, as evident, is widely used to fabricate coins. Technically, coning is implemented in any case when a manufacturer needs a sheet metal to be stamped. The working principle of the method is forcing a sheet metal into the bottom dies with up to 30 times more pressure than during air-bending.
Coining in Sheet Metal Air Bending. Compared to bottoming and coining, air bending is a less accurate technique that is also susceptible to spring back. Nonetheless, it is easy to use since you do not employ tools. In this process, a punch applies pressure to the sheet metal part in the die cavity. During the bending process, the metal part .
The coining pressure can be applied to the sheet metal at BDC by using the stationary function. This type of motion, called “dwell motion,” has three segments: rising, long dwell, and descent. For a metal forming process, the long dwell time results in uniform metal deformation. The Global Sheet Metal Coining Service Market Size Outlook [2024-2032] - In 2024, Global Sheet Metal Coining Service Market Size achieved USD XX.X Million.
Sheet metal defects affect the appearance, function or structural integrity of the sheet metal. Learn the defects and avoid them in the sheet metal process. . the metal sheet is bent into the desired shape. Forming methods include air bending, coining, and roll forming. Joining. It is the process of assembling different sheet metal components .
sheet metal coining process

the bending radius of fiber is 10 times the diameter of the cable when not under load and 20 times the diameter of the cable when under load. generally the minimum pull box size .
sheet metal coining|lancing process in sheet metal